Best Lean Manufacturing Practices
Truly perfect lean manufacturing is a goal that many companies strive for but is ultimately impossible to achieve. Workflows are constantly changing as your business and production environment changes, which means there will always be room for improvement. To address these problems, many companies want to overhaul their entire system, changing entire work processes in the blink of an eye. Now, if your company is already having major problems and errors, then a complete system overhaul could be what is needed. But for most good businesses, completely changing the way of your order processing could cause catastrophic problems in all areas of your business. That is why the main principles of lean manufacturing focus on making smaller changes to your already existing work processes to slowly but surely make your workflow as smooth and efficient as possible. However, these small, beneficial changes will only move toward maximum productivity if these changes are constantly adhered to and built upon one another. Lean manufacturing is not easy. That is why many companies spend millions and millions of dollars for 3rd party lean experts to help improve their systems. Not that this practice is wrong, but we believe that no one knows how your business like you do. And the best way to help yourself help your company is by understanding the principles of lean manufacturing. These concepts are the basic foundation to eliminate waste from your manufacturing process and can provide you with the tools to begin your lean manufacturing journey.
Continuous Improvement (Kaizen)
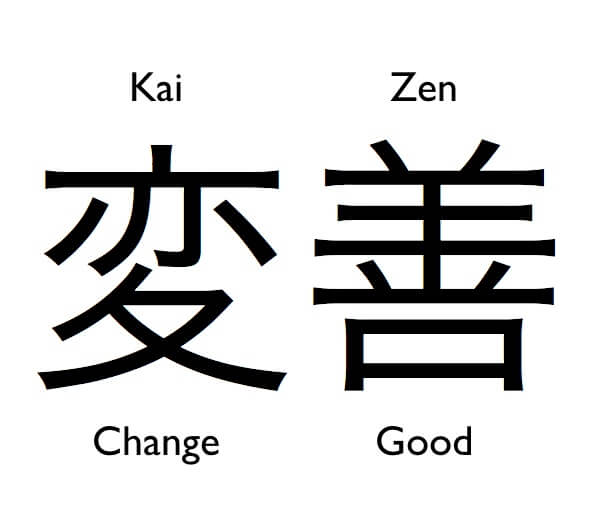
The first principle that we are going to talk about is one of the main pillars of lean manufacturing, continuous improvement or Kaizen. In a business environment, Kaizen refers to the act of “continuously improving” all functions throughout an entire company. For a little bit of background, Kaizen comes from the Japanese, “Kai” meaning “change,” and “Zen” meaning “good.” Kaizen, at its very core, is a philosophy to involve all the employees of a company to actively work towards making small improvements in everyday manufacturing processes. These changes do not just have to happen on the facility floor either. Kaizen should be implemented in and affect all departments of your organization. Implementing this strategy company-wide does two things to help improve the efficiency in your workplace. First, this policy will allow you to gradually improve all areas of your business, even parts you did not realize had problems. In your manufacturing department, you could reorganize your facility to better suit your manufacturing processes, shortening walking distances or increasing total operational area. However, even in areas like sales or accounting, balancing workloads or changing work sequences could cut operations by a fraction of the original time. But, you may be wondering, how can I get this accomplished? Second, and possibly more importantly, Kaizen is centered around actively involving all employees to make these improvements. And everyone means everyone. All employees from the CEO to the people working hands-on with the product because in Kaizen all employees’ suggestions are equally important. Having everyone involved in this exercise allows you to see potential problems in workflow from all angles of the organization. If the facility manager is noticing production times are down, he may think adding more men to the floor would be the best solution to provide more help with production. But the real problem could be that machinery is not pushing materials through fast enough, or they have a heavily convoluted workflow order. People working hands-on on the product may be able to see these problems and solutions, while the person above them may overlook them.
Reduction and Elimination of Wastefulness
Next one of the most important parts of Kaizen and the key to lean manufacturing is the reduction and elimination of waste in your workflow and facility. Typically, when a person thinks of waste, a few things come to mind: an empty soda can, an apple core, metal shavings, or expired food. However, waste, especially in a business environment can take many forms.
“The 7 Wastes” is a common way of understanding and explaining the most common wastes companies run into in a manufacturing environment.
1. Transportation:
Unnecessary movement of parts between processes and complex material flow paths.
The unnecessary transportation of materials and goods throughout a facility might seem like an obvious waste at first, but is probably one of the easiest to overlook and hardest to overcome. Typically, a facility is laid out logistically with a specific goal in mind, whatever that is. Materials are stored in a convenient area, production may be placed nearby, and you could have shipping at the end to create a nice little assembly line-like environment. However, as businesses grow and work processes have to be expanded to accommodate more and more production, extra storage area might have to be added around beside shipping to ensure that products can be manufactured at a proper pace. The only problem is the original storage area allowed for easy access to materials, but now materials have two or three times the transportation cost due to overcrowding. These problems can sometimes not be addressed due to the huge initial cost to move around machinery or storage. Transporting equipment to adapt to a new facility layout or new work process can cost a lot of time and potentially hold up production, same for moving material storage. However, looking at the basis of lean manufacturing, you want to focus on the small benefits or increases in productivity that will compound over a period of time.
2. Motion:
Occurs when individuals move more than is necessary for the process to be completed.
Similar to the waste of Transportation, the waste of motion occurs whenever an employee has to incur extra movement to complete a task. In this type of waste, it relates to pretty much all types of movement for a regular employee, including walking, reaching, lifting, and bending. Similar to waste of transportation, waste of motion can oftentimes be overlooked because the work process has “always been the way they have done it.” Employees may not realize that the simple repositioning of materials or switching the location of certain offices may undoubtedly allow for entire processes to run more quickly due to a decrease in motion.
3. Overproduction
Manufacturing too much, too early or “Just in Case” discouraging smooth flow.
Overall, overproduction violates many of the basic rules of lean manufacturing. Overproduction, by definition, leads to excess inventory for a company. Two of the biggest physical costs of overproduction are the storage and movement of inventory. Now, you may be thinking, “having excess inventory is a good thing in case a huge order comes through.” Then you would be falling into the “Just in Case” fallacy. Companies who subscribe to this belief will incur higher holding costs for their inventory because they do not believe in their work processes to keep supply equal to demand. In the perfectly lean manufacturing environment, a company would practice “Just in Time” manufacturing, producing your product just in time for it to be used by the customer. This practice ensures that your work in progress does not build up between processes, and it is not important to run the machine all day, as fast as it will go. The idea is a company wants to do whatever it takes to minimize the time it takes to complete a project and make those projects as simple as possible.
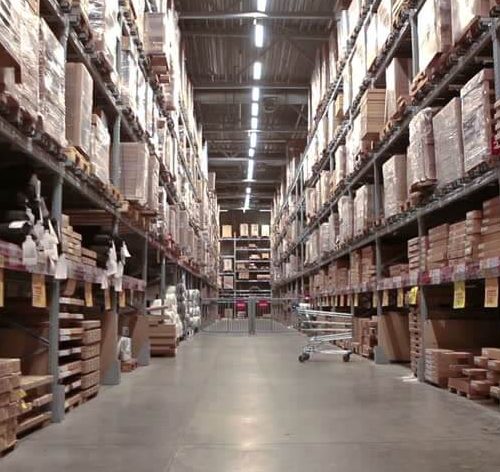
4. Inventory (Work In Progress)
Any raw material, work in progress or finished goods which are not having value added
A direct result of overproduction, excess inventory is ultimately bad for business due to what it means for management costs and inventory turnover. Ultimately, mirroring our quote, inventory provides no additional value to the company that a JIT manufactured good would not also provide. However, in the case of excess inventory, you will incur additional costs in the form of space problems, if the excess inventory is stored in your facility, it very well may disrupt work processes. Plus, this inventory will almost always lead to a decrease in profit that you see from the product. This may happen in a number for a number of different reasons. The overstocked products are oftentimes forced to be sold at a discount to clear out space, lowering your margin on the product. Plus, you will, of course, incur the cost to store the inventory and whatever cost to maintain them before they are sold.
5. Waiting
Idle time is produced when two interdependent processes are completely synchronized
The waste of waiting can occur all throughout a product’s life-cycle and is typically the result of mismanaged or poor flowing processes. Overall, product and materials waiting to move from one process to another obstructs the flow of work processes and equates to a slowdown in overall manufacturing time. By most estimations, as much as 99% of any product’s manufacturing time is spent in the waiting process, either waiting to be manufactured, waiting to move from one stage to another, or waiting to be shipped to the customer. The biggest downfall of the waste of waiting similar to the waste of inventory in that these products are having no value added to them. They are only taking up space, time, and cost.
6. Over-Processing:
Processing beyond the standard required by the customer
For this waste, it is important to not confuse over-processing with not caring about customer satisfaction. Looking at “Processing beyond the standard required by the customer,” many will think that this equates to “doing the bare minimum for your customer.” But it does not. It simply refers to using simpler and more appropriate machinery and tools to complete a job instead of more expensive and complex machinery. We do not want overkill. There is no need to “use a sledgehammer to crack a walnut.”
7. Defect
A component which the customer would deem unacceptable to pass the quality standard
Probably the most obvious classification of waste, defects can first cause companies to waste money on materials, but that only occurs when the defect is noticed in the manufacturing stage. They can also cause businesses to refund previous purchases when the defect goes unnoticed or even mass product recalls when the defect affects every product produced. In order to combat this problem, companies that are unable to “perfect” their manufacturing processes also have to spend time and money inspecting and reviewing projects extensively for flaws.
When thinking about waste in your manufacturing process, always go the way of Antoine de Saint-Exupery,
“Perfection is achieved not when there is nothing more to add, but when there is nothing left to take away."
Standardized Work
So, you have identified and minimized your 7 types of waste and made small beneficial changes to improve your manufacturing processes. Great! However, these changes will not provide any advantage in the long run if these work processes are not standardized, kept in place, and strictly adhered to. Easier said than done. But there are a few methods and steps that you can use to help institute these processes full time. Training, first and foremost, goes a long way in ensuring your new work processes are carried out correctly. But perhaps more importantly, it will help your employees understand Why things are done this way and Why this is the best way to do it. Because having new Kaizen is great, but it does nothing to help if no one knows why the change was made or how to carry it out. Also, team training and improvement exercises go a long way in allowing new and old employees to figure out the best way to work with one another, seeing each other’s strengths and weaknesses. Breaking tasks into smaller steps can be a great way to promote standardization throughout a manufacturing process. By doing this, you can time each step in the process multiple times in order to get a standard working time for a particular task. This helps you in a variety of different areas but most importantly planning project manufacturing times. Striving for Just-In-Time inventory, you will be able to much more accurately predict your project timeline and know when to start the project to have it finished right when it is supposed to be shipped out the door. This type of forecasting can be invaluable to your lean manufacturing efforts. After segmenting your manufacturing process, it is important to look at and analyze your findings. Ensure to take multiple measurements (10 minimum) of each step in the process to minimize variability. Verify these are the best methods with all employees, across all shifts and plant areas. Finally, document the best methods in a common format. However, it is important to never allow yourself or your company to become complacent in your manufacturing process. Like we stated earlier in the Kaizen section, there is no such thing as a perfect process. Things change, technology improves, and new ideas are born every day. Make sure to continue your kaizen efforts through standardization as this is the best way to ease growing pains as your company expands.
Operating Efficiency
Finally, we are going to talk about operating efficiency. The overall goal of lean manufacturing is to obtain the highest operating efficiency possible for your company. Simply put, it is the output that a company produces versus the input needed to run the company. Now for many people this only means one scenario, cutting your costs while keeping production constant. However, this type of thinking can lead companies into many different pitfalls just trying to “raise the bottom line.” Many of the common “quick” ways to cut cost can lead may lead to problems down the road in the form of lower employee moral or even poor customer service and support, even if these things do not happen right away. In order to cut costs the correct way, supervisors must put in their homework to find inefficiencies in their processes, products, people, and purchasing. Otherwise, they run a very high risk of spreading their resources too thin, exhausting their employees and company as a whole. Or, as a company, you under produce entirely, creating longer project lead times and potentially losing profits and customers. However, there are additional options for companies looking to increase operating efficiency. The first is getting more production while using the same resources, which hopefully comes in the form of repeated kaizens and standardization. Otherwise, you can fall into the same trap as someone cutting costs and stretching resources. It is best to let this process occur naturally (or rather with the guiding hand of lean manufacturing). This way, as you and your team are constantly finding ways to streamline your work processes and reduce waste in manufacturing, production will rise as a result. Your management and employees will gain a better understanding of the overall work processes (as Kaizen involves all employees), and the company as a whole will have an easier time estimating project timelines The second option is producing MUCH more product while providing more input. For this option, it is important to see a clear opportunity for your business to succeed, as it typically requires a large investment in some form or another. For example, a family owned business that has worked out of the same facility for 50 years may have outgrown their area, slowing down their manufacturing processes. Building a new facility with a clear and efficient magnification process layout would be a huge undertaking. However, being able to produce the product cheaper and quicker could potentially more than make-up for the huge investment in a new facility, making this a smart move. Each of these options can allow a company to become leaner; it just depends on which one is right for you.
Panel Built's Practices
Panel Built strives for constant improvement in all aspects of our business from top to bottom. Panel Built Manufacturing is a constantly improving process of making a variety of quality products, with the most effective use of time, material, equipment, space, and effort. We have implemented many of the aspects of lean manufacturing to our own work and manufacturing process, as well as developing key manufacturing tactics to help ensure this mentality permeates through all of our projects. Tools like Kaizen, the 5S Approach for organizing the workplace (Sort, Straighten, Scrub, Spread, and Systematize), Poka Yoke (error proofing), and Kanban (System for JIT inventory), allow us to push closer to a system that is as efficient as possible. However, another benefit of our lean manufacturing practices is that it inspires our entire team to invest themselves into the company. With every work day, employees are encouraged to find new and more efficient ways to improve our day to day processes. This challenges each member of our company to think critically about their jobs, about our products, and about our processes as a whole, providing them with a greater understanding of our products and our goals.
"Panel Built has very strong beliefs and philosophies. The first is that customer service is our highest priority. Everything we do, should be done with the thought of how will this best serve our customers.
Our next belief is that we must always be improving. If we are not improving, we are not doing our best for our customers. We are in the business of solving people's space needs. They depend on us to be the experts. To be the expert at anything, you must have knowledge and skills, and passionately pursue excellence."
-Mike Kiernan, President of Panel Built, Inc.