Using The Hierarchy Of Controls To Maximize Safety
Employee health and safety is one of the main areas of concern for businesses. In fact, the United States dedicates over half a Billion dollars in funding every year to help ensure the safety of all country’s employees (public and private) through OSHA, the Occupational Safety and Health Administration. You have likely heard of them.
One of the ways that OSHA goes about helping companies and their employees work safer everyday is by providing a variety of health and safety guidelines to follow. At the core of OSHA’s Safety and Health Program guidelines is Hazard Prevention and Control (before Hazard Control comes Hazard Identification). Luckily, our friends at the Department of Labor have provided us with a variety of helpful tools in order to minimize the risk involved with workplace hazards, among these is The Hierarchy of Hazard Controls.
The Hierarchy of Hazard Controls is a helpful step by step guide for organizations that help them reduce hazard risks. Using the Hierarchy of Controls, organizations (which have identified the hazards in their facility) can start at the top of the ‘Control Pyramid’ and work their way down till they find a solution. Always Start at The Top. The levels of the hierarchy are arranged from most effective to least effective. You should not try and solve a hazard issue unless all levels above it have been exhausted. With that said, let’s look at the first level of the Hierarchy…
Hazard Control Through Elimination
Starting at the top, the first level of the hierarchy of controls is hazard control through Elimination. Elimination is the most effective form of hazard control because it removes the threat all together from the plant. One of the most common issues with the elimination level of hazard control is that it could also be considered one of the most difficult to implement. Oftentimes, the object or thing that is causing the hazard is also an important part of a work process. For this reason, it is recommended to implement this control in the design phase of your facility. By eliminating the hazard from the start, your facility does not have to incur downtimes in work processes or the retraining employees to eliminate the hazard.
One of the main examples used to show the Elimination control is an employee working from a considerable height. Having employees work at high levels creates a fall hazard. By shifting the work process to ground level, the threat of a dangerous fall is eliminated. This is more effective than using a harness or any other fall protection because the threat has been reduced 100%. Other examples of hazard control through elimination include the removal machinery that emits dangerous or painful noise levels or scrapping old equipment with a tendency to malfunction.
Hazard Control Through Substitution
The next level down in the hierarchy of controls is hazard control through Substitution. This level of the hierarchy acts similarly to the Elimination by removing the initial hazard, but in this case, you are replacing it with another. It is important that the substitute Does Not Cause the Same Hazard and Does Not Create A New Hazard. Also, like Elimination, Substitution is most effective when incorporated into the initial design of a work process. Ideally, hazard control through substitution would be equally as effective as elimination. However, when introducing the substitute, unforeseen new hazards can present themselves in the future, even if proper vetting has gone into choosing the substitute.
The most common example of substitution is replacing a toxic chemical for a non-toxic one. The substituted chemical should create a much safer scenario should it come in contact with an employee, but the new chemical could have unanticipated consequences later are that are not currently known. Proof of this can been seen on the Hazard substitution Wikipedia page, under the section labeled ‘Regrettable substitutions.’
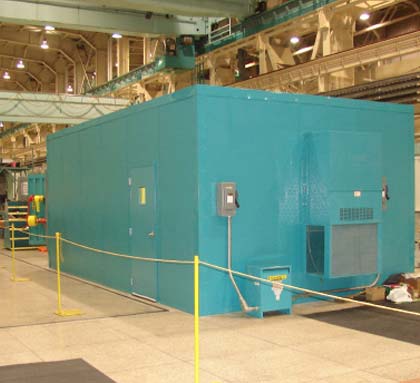
Hazard Control Through Engineering
The next level of the Hierarchy of Controls is hazard control through Engineering. This level of the Hierarchy will be used whenever the hazard is necessary to operation and cannot be removed through elimination or substitution. Engineering involves controlling the hazard by creating a barrier between the hazard and the employees or by diverting the hazard away from employees. In many cases, this will involve an enclosure to be made around the hazard as the barrier or for an exhaust hood to be installed to divert dangerous fumes, powders, or flakes.
For example, at Panel Built, one of our most popular product lines are our machine enclosures. One of the main reasons that companies decide to enclose a piece of machinery is to help reduce the noise output to the rest of the facility. As we mentioned in the earlier levels, ideally these machines would be removed or replaced, but if neither of these are viable options, engineering a machine enclosure to reduce the noise can be the next best option. However, these enclosures can be used as barriers of other sorts as well, controlling heat output from machinery, collecting dust and debris from milling work (via an incorporated ventilation system), or even just keeping employees out of a potentially dangerous situation.
Hazard Control Through Administration
The next level of the Hierarchy of Controls is hazard control through Administration. This level controls hazards through procedures and policies that a company implements within their facility. There are a variety of forms that administrative controls can take. The main methods that can be seen in facilities throughout the United States are hazard control through signage, restricted access, or employee training.
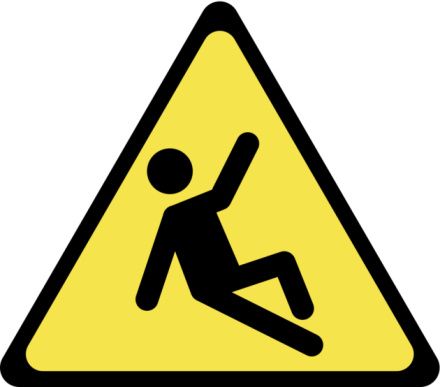
For signage, these will typically be warnings or cautions that a company will have posted within their facility, typically in breakrooms or employee common areas. These signs can range from ‘FLAMMABLE’ signs to ‘Employees Must Wash Hands.’ Restricted Areas are typically related to areas where only authorized personnel are allowed due to hazardous chemicals or machinery. And finally, employee training can include anything from learning proper lifting technique to identifying potential hazards to being able to properly operate a piece of machinery. All of these are administrative controls that help create a safer working environment by providing additional information to employees. The main downside to administrative control is that they require active thinking and are susceptible to human error.
Hazard Control Through Personal Protective Equipment
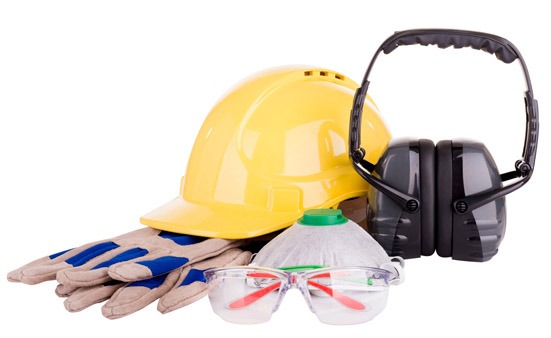
The final level of the Hierarchy of Control is Personal Protective Equipment or PPE. This is the form of hazard control that most workers will be familiar with, not because it is the most often used, but because it is the most noticeable. PPE can be goggles, special clothing, gloves, helmets, earbuds, and more that a person wears on their body that protects them from a hazard. The use of PPE is used whenever there is no other way to mitigate the risk involved with a hazard, which is why it is the last level on the Hierarchy of Hazard Controls. However, this does not make PPE a bad thing, of course. In fact, PPE is vital to keeping a safe workplace.
PPE protects both the short term and long-term health and safety of an employee. Equipment like eye protection and hard hats provides additional protection to sensitive areas of a person that are susceptible to falling objects or debris from grinding, keeping employees safe on a day to day basis. While other pieces of equipment, like respirators or earbuds protect the long term health of employees by keeping air particles out of their lungs and reducing hearing loss respectively.
Overall, all of these levels of the hierarchy of control are important to keeping a safe workplace. They are all methods utilized in “Prevention through design” which is a method of minimizing the risk of workplace hazards early in the formation of a facility or work processes. Prevention through design is a way for companies to layout their facilities, equipment, work processes, and more to remove as many hazards as possible. This method uses elimination and substitution in order to rely less heavily on other controls, reducing the risk of human or operator error in relation to a hazard. However, as we have seen, some hazards are inevitable in a facility, in which case Engineering, Administrative, and PPE controls provide a variety of ways to keep employees as safe as possible.